Selecting the appropriate mechanical seal is crucial for ensuring reliable and safe operation of pumping equipment. Failure to choose the right seal type can lead to leakage, equipment damage, and hazardous conditions. This document provides an in-depth comparison of single and double mechanical seals, examining their design, working principles, and applications to facilitate informed decision-making for various industrial scenarios.
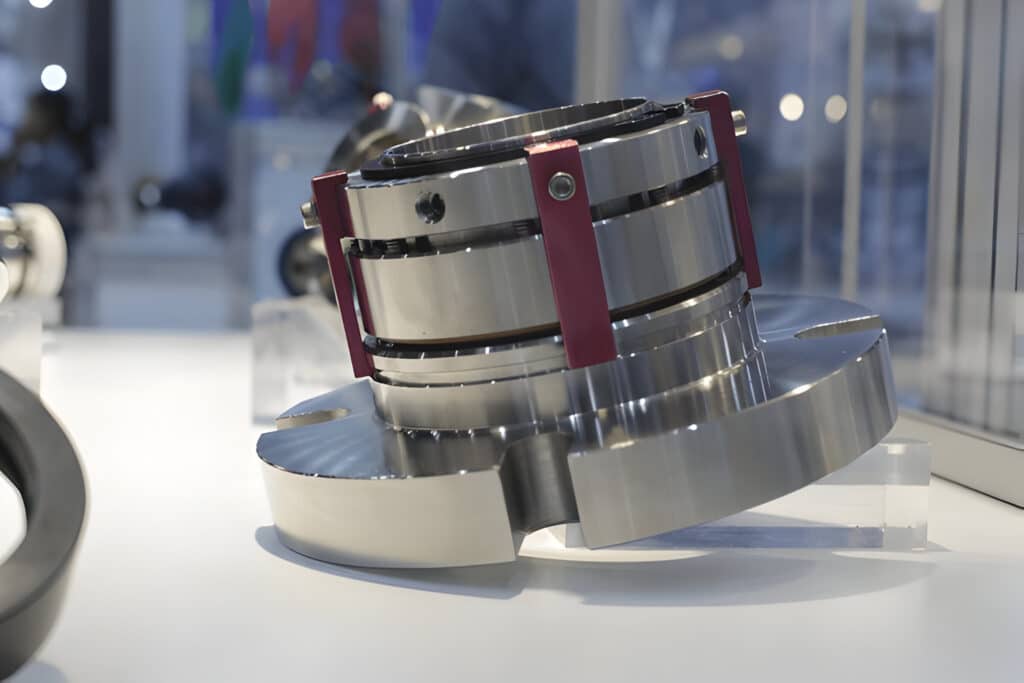
Single Mechanical Seals
The characteristic of a single mechanical seal is its relatively simple design, including two main components: a rotating ring fixed on the equipment’s rotating shaft and a stationary ring firmly installed on the equipment housing. These rings are manufactured with very flat, precisely ground surfaces that contact to form the primary sealing interface.
To maintain consistent contact between these faces, a spring mechanism (or bellows in some designs) applies force to press the rotating and stationary rings together. The spring is typically located on the atmospheric side of the seal, protected from the process fluid. Secondary sealing elements like O-rings or gaskets are used to seal between the stationary parts and the seal housing.
How Single Mechanical Seals Work
The working principle of a single mechanical seal relies on the formation of an extremely thin film of process fluid between the precisely ground sealing faces, typically only a few microns thick. When the equipment is operating, the rotating ring spins with the shaft while the stationary ring remains fixed to the housing.
The sealing effect is the result of a balance between the closing force provided by the spring and fluid hydraulics, and the opening force produced by the pressure of the fluid film itself. The spring force squeezes the faces together while the fluid pressure in the thin film tries to push them apart. Equilibrium is reached when a stable fluid film is established.
When fluid migrates from the high-pressure side to the low-pressure atmospheric side, there is typically a minimal amount of vapor leakage at the sealing faces. This small leakage is normal and necessary to lubricate and cool the faces. Seal failure can occur if the faces run too hot and dry or if the film breaks down due to contamination or loss of fluid properties.
Applications of Single Mechanical Seals
Single mechanical seals are primarily used in situations where the pumped fluid poses minimal risk to the environment or to personnel operating the equipment. They are well-suited for general industrial applications involving fluids that are compatible with the sealing materials, relatively clean, and not considered seriously hazardous.
Some typical applications for single mechanical seals include:
- Water and wastewater pumps
- Food processing (milk, beverages, animal fats)
- HVAC and cooling tower pumps
- General chemical transfer with benign fluids
- Low-pressure hydrocarbon services
In chemical processing, petroleum, and petrochemical industries, single mechanical seals are frequently used for a wide range of utility applications where the handled fluids are less critical in terms of potential hazards or environmental impact. For more demanding duties involving dangerous, flammable, or environmentally sensitive fluids, double mechanical seals are often specified to provide an extra layer of protection and redundancy.
Double Mechanical Seals
Double mechanical seals are a more advanced and robust sealing solution compared to single seals. They consist of two single mechanical seals arranged in series, providing an additional layer of protection against leakage and failure.
The two main components of a double seal are the inner (primary) seal and the outer (secondary) seal. The inner seal is positioned closer to the process fluid being sealed, while the outer seal is located on the atmospheric side of the assembly. Between these two seals, there is a cavity that is filled with either a buffer fluid or a barrier fluid.
The presence of this fluid-filled cavity is a defining feature of double mechanical seals. It serves several important functions, such as lubricating the seal faces, dissipating heat, and preventing the ingress of contaminants. The fluid is typically circulated and maintained using an external support system, which may include a reservoir, pumps, heat exchangers, and monitoring devices.
How do Double Mechanical Seals Work
The operation of double mechanical seals relies on a two-stage sealing mechanism. The inner seal’s primary role is to contain the process fluid within the pump or equipment casing, preventing it from leaking out. It acts as the first line of defense against leakage and is designed to withstand the full pressure and temperature of the process fluid.
The outer seal, on the other hand, has two main functions. First, it serves to contain the buffer or barrier fluid within the cavity between the seals. Second, it acts as a backup seal, capturing any minor leakage that may occur past the inner seal and preventing it from escaping to the atmosphere.
The pressure of the fluid in the cavity plays a crucial role in the sealing performance of double seals. When using a buffer fluid, its pressure is typically maintained at a level lower than the process fluid pressure. In this configuration, the buffer fluid captures and contains any leakage from the inner seal, preventing it from reaching the outer seal or the environment.
Alternatively, when using a barrier fluid, its pressure is usually kept higher than the process fluid pressure. This creates a complete physical barrier between the process fluid and the atmosphere. If any leakage occurs through the inner seal, it is directed back into the process fluid rather than escaping to the outside.
Types of Double Mechanical Seal Arrangements
Back-to-Back Arrangement
In a back-to-back arrangement, the rotating faces of the two seals are oriented away from each other. This creates a cavity between the seals where a barrier fluid, pressurized higher than the seal chamber pressure, can circulate.
The barrier fluid provides lubrication to the seal faces and absorbs any leakage that may occur. This arrangement is well-suited for applications involving volatile, hazardous, or expensive process fluids, as it effectively contains any leakage within the barrier fluid system.
Back-to-back seals offer excellent sealing performance and full pressure backup capability within a relatively compact axial length. However, they may be more costly compared to single or tandem seals and require more axial space in certain installations.
It’s important to note that while a loss of barrier fluid will keep both seals closed, a failure of the inner seal can lead to contamination of the process fluid by the barrier fluid. Additionally, the outer seal faces in a back-to-back configuration typically have a lower pressure rating compared to the inner seal faces.
Tandem (Face-to-Face) Arrangement
A tandem arrangement, also known as a face-to-face arrangement, has both seals oriented in the same direction, installed in series. The inner (primary) seal handles the full pressure of the process fluid, while the outer (secondary) seal serves as a backup.
In this configuration, a buffer fluid, maintained at a lower pressure than the process fluid, circulates between the two seals. Tandem seals are preferred for sealing toxic, hazardous fluids and gases, as well as for handling solids and contaminated media. They also exhibit better tolerance to shaft misalignment compared to other arrangements.
However, tandem seals generally require more axial space and increase the overall system complexity and cost. If the inner seal fails, the outer seal becomes the sole barrier preventing leakage, and its sealing performance may be inferior compared to a back-to-back arrangement.
Face-to-Face Arrangement
The face-to-face arrangement positions the rotating faces of the two seals toward each other, forming a sealed chamber between them. This design can utilize either buffer or barrier fluid and often employs a shared stationary component for both seals.
Face-to-face seals are particularly useful in equipment with limited space constraints and can effectively handle solids and contaminated media. They are also capable of tolerating reverse pressure situations. The compact and simple design allows for more axial travel, and in some cases, the barrier fluid can act as a coolant.
A significant drawback of face-to-face seals is that the outer seal cannot provide full-pressure backup. Moreover, the reliance on a common stationary component means that a failure of this component could lead to the failure of both seals.
The Differences Between Single and Double Mechanical Seals
Feature | Single Mechanical Seal | Double Mechanical Seal |
---|---|---|
Number of Seals | One | Two |
Number of Sealing Faces | Two | Four |
Complexity | Simpler | More Complex |
Lubrication and Cooling | Typically relies on process fluid | Dedicated buffer or barrier fluid |
Need for Support System | Generally not required | Typically required for buffer / barrier fluid |
Primary Applications | Less demanding, non-hazardous fluids | Hazardous, toxic, high-pressure, critical applications |
Cost (Initial) | Lower | Higher |
Leakage Potential | Higher | Lower |
Suitability for Hazardous Fluids | Limited | High |
Common Configurations | Pusher, Non-pusher | Back-to-Back, Tandem (Face-to-Back), Face-to-Face |