Rubber bellow mechanical seals are essential components in various industrial applications. They play a crucial role in preventing leakage and ensuring the smooth operation of rotating equipment.
In this comprehensive guide, we will explore what rubber bellow mechanical seals are, their function, and how they work. We will also delve into the components and materials used in these seals and discuss the advantages they offer over other sealing solutions.
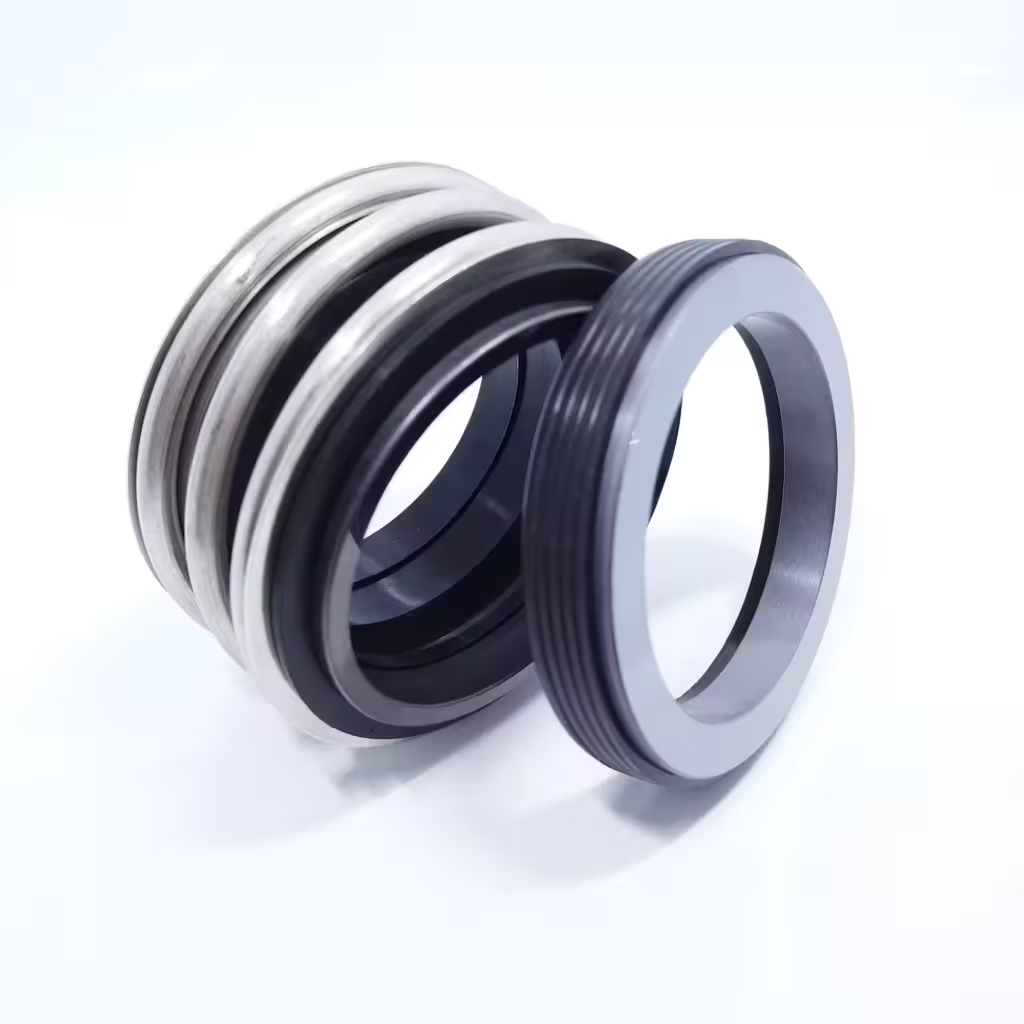
What Are Rubber Bellow Mechanical Seals
Rubber bellow mechanical seals are a type of specialized sealing solution designed to prevent leakage and ensure efficient operation in various industrial applications, such as water pumps, chemical pumps, and automotive pumps.
Rubber bellow mechanical seals consist of a flexible rubber bellow that acts as a sealing element between rotating shafts and stationary components. The bellow is typically made from high-quality, durable rubber materials that are compatible with the media being sealed. This ideal seal material allows for some degree of seal misalignment and provides excellent sealing capabilities in both stationary and rotating applications.
The rubber bellow seal design incorporates a single pusher-type seal arrangement, which includes a conical spring that maintains a consistent sealing force. This unique configuration eliminates the need for shaft fretting and ensures a stable seal-to-shaft interface, resulting in extended service life and improved mechanical seal reliability.
What Is the Function of Rubber Bellow Mechanical Seals
The primary function of rubber bellow mechanical seals is to prevent leakage of process fluids while simultaneously shielding the shaft and bearings from contamination.
By providing a reliable, flexible sealing solution, rubber bellow mechanical seals help maintain the integrity and performance of the equipment. These seals are designed to accommodate minor shaft misalignment and axial movement, ensuring a consistent seal even under challenging operating conditions.
How Do Rubber Bellow Mechanical Seals Work
Rubber bellow mechanical seals are a type of single pusher-type seal that utilizes a conical spring to maintain contact between the seal faces. The spring, located on the product side, provides axial force to keep the rotating and stationary faces pressed together.
The sealing action occurs between the rotating face, which is typically made of a hard material such as silicon carbide or tungsten carbide, and the stationary face, usually made of a softer material like carbon or graphite. As the shaft rotates, the spring maintains a constant pressure between the faces, preventing leakage of the process fluid. The rubber bellows, often made of high-quality elastomers such as FKM or EPDM, provide a flexible connection between the rotating and stationary components, accommodating any shaft movement or vibration.
Components and Materials of Rubber Bellow Mechanical Seals
- Bellows: The flexible rubber bellows are the key component of rubber bellow mechanical seals. They are typically made from high-quality, durable elastomers such as FKM (Viton), EPDM, or NBR (Nitrile). The bellows provide a leak-tight seal while accommodating shaft misalignment and axial movement.
- Seal Faces: The primary seal faces are responsible for creating the main sealing interface. These faces are usually made from hard, wear-resistant materials such as silicon carbide, tungsten carbide, or carbon graphite. The seal faces are precision-lapped to ensure a smooth, flat sealing surface.
- Springs: Single or multiple springs, often made from stainless steel, are used to maintain a constant closing force on the seal faces. The springs compensate for wear and thermal expansion, ensuring consistent sealing performance throughout the seal’s service life. Conical springs are commonly used in rubber bellow seals for their compact design and uniform load distribution.
- Retainer and Gland Plate: The retainer and gland plate, typically made from stainless steel or other corrosion-resistant alloys, hold the seal components in place and provide a connection point to the equipment being sealed.
- Drive Collar: The drive collar, also made from stainless steel or similar materials, is attached to the rotating shaft and transmits torque to the rotating seal face. It is designed to minimize shaft fretting and wear, extending the seal’s service life.
- Secondary Seals: O-rings or other types of secondary seals, made from compatible elastomers, are used to prevent leakage between the stationary and rotating components of the seal assembly.
Advantages of Rubber Bellow Mechanical Seals
- Enhanced Sealing Performance: Rubber bellow mechanical seals provide superior sealing capabilities compared to traditional seals. The flexible rubber bellows allow the seal to maintain contact with the shaft, even in the presence of misalignment or vibration. This ensures a leak-free operation and prevents the ingress of contaminants.
- Improved Shaft Protection: The rubber bellows act as a barrier between the sealed fluid and the shaft, preventing direct contact and minimizing shaft fretting. This protection extends the service life of the shaft and reduces maintenance requirements. The lack of shaft damage also contributes to improved seal reliability and performance.
- Ease of Installation: Rubber bellow mechanical seals are designed for simple and quick installation. The seal assembly is typically supplied as a pre-assembled cartridge unit, which can be easily fitted onto the shaft without the need for complex alignment procedures. This ease of installation reduces downtime and minimizes the risk of incorrect product selection or installation errors.
- Versatile Application Range: These seals are suitable for a wide range of industrial applications, including water pumps, chemical pumps, and automobile pumps. They can handle various fluids, from clean liquids to abrasive slurries, and operate effectively in both high and low-pressure environments.
- Compact and Space-Saving Design: Rubber bellow seals feature a slimeline design that requires minimal space in the seal chamber. This compact profile allows for greater flexibility in equipment design and enables the seals to fit into tight spaces where other seal types may not be suitable.
- Cost-Effective Solution: Compared to other mechanical seal designs, rubber bellow seals offer a cost-effective sealing solution. The simplicity of their design, combined with the use of high-quality yet affordable materials, makes them an economical choice for many industrial applications.
- Ability to Handle Pressure Fluctuations: Rubber bellow mechanical seals are designed to handle pressure fluctuations and reversals effectively. The flexible bellows allow the seal to maintain a stable sealing interface even when subjected to varying pressure conditions. This ability to adapt to pressure changes ensures reliable sealing performance and prevents leakage during dynamic operating conditions.
FAQs
What materials are used to manufacture rubber bellow mechanical seals?
Rubber bellow mechanical seals are typically made from high-quality elastomers, such as nitrile (NBR), ethylene propylene diene monomer (EPDM), fluoroelastomers (FKM), and perfluoroelastomers (FFKM), depending on the application requirements and the type of media being sealed.
How do you select the right rubber bellow mechanical seal for an application?
When selecting a rubber bellow mechanical seal, consider factors such as the type of media being sealed, operating temperature and pressure, shaft speed and diameter, the presence of abrasive particles, and chemical compatibility to ensure optimal performance and longevity.
What are the common failure modes of rubber bellow mechanical seals?
Common failure modes of rubber bellow mechanical seals include abrasion, chemical degradation, thermal damage, improper installation, and mechanical damage due to misalignment or excessive shaft movement.
How do rubber bellow mechanical seals compare to other types of mechanical seals?
Rubber bellow mechanical seals offer several advantages over other types of mechanical seals, such as better accommodating misalignment and shaft movement, lower cost, and resistance to abrasion and corrosion. However, they may have limitations in high-temperature or high-pressure applications, where other types of seals, such as metal bellows or cartridge seals, may be more suitable.