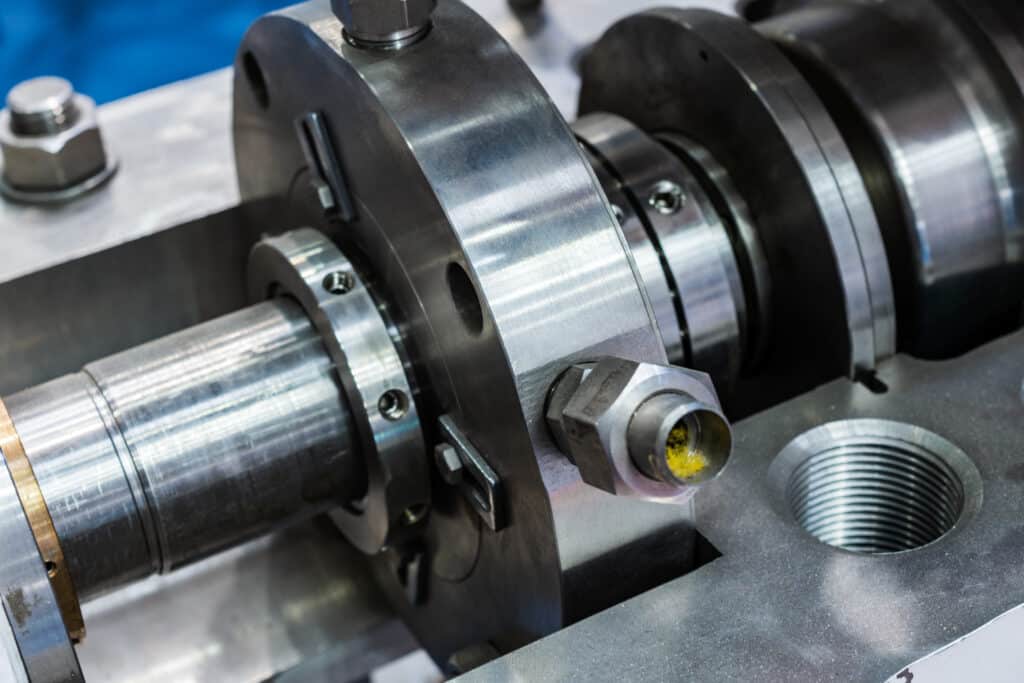
What Is Mechanical Seal for High Temperature
A mechanical seal for high temperature is a critical component in rotating equipment that operates in extreme heat conditions. These specialized seals are designed to withstand elevated temperatures while maintaining their sealing effectiveness, preventing leakage, and ensuring reliable operation. High-temperature mechanical seals find applications in various industries, including oil and gas, chemical processing, power generation, and aerospace.
High-temperature mechanical seals are engineered to tackle the unique challenges posed by elevated temperature environments. They must contend with thermal expansion, material degradation, fluid vaporization, and potential coking or fouling of seal components. To address these issues, high-temperature seals incorporate features such as balanced seal faces, floating components, and advanced material combinations that can withstand extreme heat and maintain their dimensional stability.
Challenges of High-Temperature Environments on Mechanical Seals
Material Degradation
Elevated temperatures can cause seal materials to degrade, lose mechanical properties, and fail prematurely. Polymers, elastomers, and even metals can soften, embrittle, or undergo chemical changes at high temperatures, compromising sealing performance.
Thermal Expansion and Mechanical Deformation
Temperature fluctuations and gradients can lead to differential thermal expansion between seal components and adjoining equipment. This can result in mechanical deformation, loss of sealing contact, and leakage paths.
Fluid Vaporization and Dry Running
High-temperature fluids are prone to vaporization, especially at the sealing interface. Vaporization can lead to dry running conditions, increased wear, and seal failure. Maintaining a stable fluid film is critical for seal lubrication and heat dissipation.
Coking and Fouling of Seal Components
Certain high-temperature fluids, such as hydrocarbons, can undergo coking or leave deposits on seal faces and components. Coking and fouling disrupt the sealing interface, cause abrasive wear, and impair seal performance.
Key Factors in Selecting Mechanical Seals for High-Temperature Service
Process Fluid Properties
The properties of the process fluid play a crucial role in determining the appropriate mechanical seal for high-temperature service. Key considerations include the fluid’s chemical composition, viscosity, and potential for phase changes at elevated temperatures.
For example, fluids with high vapor pressures may require specialized seal designs to prevent vaporization and maintain liquid at the sealing interface. Additionally, corrosive or aggressive fluids may necessitate the use of chemically resistant seal face materials and elastomers to prevent premature failure.
Temperature Limits of Seal Materials
High-temperature environments can push seal materials to their limits, making it essential to select components that can withstand the expected operating conditions. The maximum temperature rating of seal face materials, such as silicon carbide, tungsten carbide, and carbon graphite, must be carefully evaluated to ensure they can maintain their integrity and tribological properties at the desired operating temperature.
Similarly, elastomers used in secondary seals, such as FKM, FFKM, and PTFE, should be chosen based on their temperature stability and ability to retain their sealing properties under high-temperature conditions.
Pressure Capabilities of Seal Designs
The pressure rating of a mechanical seal is another critical factor in high-temperature applications. Seal designs must be capable of withstanding the expected operating pressures without compromising the integrity of the sealing interface or allowing excessive leakage.
Back-to-back and tandem seal arrangements are often employed in high-pressure, high-temperature services to provide additional sealing redundancy and enhance pressure capabilities. The selection of seal face materials with high compressive strength and the use of robust seal housing designs can further improve the pressure performance of mechanical seals in demanding high-temperature environments.
Shaft Speed and Equipment Dynamics
The rotational speed of the equipment and the associated shaft dynamics can significantly impact the performance of mechanical seals in high-temperature applications. High shaft speeds can generate increased heat at the sealing interface due to friction, leading to accelerated wear and potential thermal distortion of seal components.
To mitigate these issues, seal designs with enhanced lubrication features, such as spiral grooves or laser-inscribed face patterns, can be employed to improve heat dissipation and maintain a stable fluid film between the seal faces. Additionally, the use of flexible graphite or Grafoil secondary seals can accommodate shaft misalignment and minimize the impact of equipment dynamics on seal performance in high-temperature service.
Mechanical Seal Types and Arrangements for High-Temperature Applications
Back-to-Back Arrangement
In a back-to-back seal arrangement, two mechanical seals are mounted with their back plates facing each other. This configuration allows for a cooling or barrier fluid to circulate between the seals, effectively managing heat dissipation.
Back-to-back seals are ideal for high-temperature applications where the process fluid is particularly hot or where thermal expansion of components is a concern. The barrier fluid helps to maintain a stable environment for the seal faces, preventing material degradation and ensuring optimal performance.
Face-to-Face Arrangement
Face-to-face seal arrangements feature two mechanical seals mounted with their seal faces oriented toward each other. This setup is beneficial in high-temperature applications where the process fluid is clean and does not pose a risk of clogging or fouling the seal components.
Face-to-face seals allow for efficient heat dissipation through the seal faces, as the cooling fluid can directly contact both sets of faces. This arrangement is often used in conjunction with a suitable piping plan to ensure proper cooling and lubrication of the seal faces.
Tandem Arrangement
Tandem seal arrangements consist of two mechanical seals mounted in series, with a buffer fluid between them. This configuration provides an additional level of protection against leakage and is commonly used in high-temperature applications where the process fluid is hazardous or environmentally sensitive.
The buffer fluid serves to lubricate and cool the seal faces, while also acting as a barrier between the process fluid and the atmosphere. Tandem seals are particularly effective in preventing fluid vaporization and dry running, as the buffer fluid maintains a liquid state even at elevated temperatures.
Material Selection Guide for High-Temperature Mechanical Seals
Face materials:
- Silicon carbide: High thermal conductivity, wear resistance, chemical compatibility, thermal shock resistance. Suitable for temperatures up to 1800°F (982°C).
- Tungsten carbide: Superior wear resistance, ideal for abrasive environments.
- Carbon graphite: Self-lubricating, thermally stable, suitable for dry running conditions and temperatures up to 1000°F (538°C).
Elastomers:
- Fluoroelastomers (FKM): Good for temperatures up to 400°F (204°C), offers good chemical resistance.
- Perfluoroelastomers (FFKM): Can handle temperatures up to 600°F (316°C), provides exceptional chemical resistance.
- Polytetrafluoroethylene (PTFE): Excellent thermal stability, low friction, chemical inertness. Suitable for temperatures up to 500°F (260°C).
Metallurgy:
- Stainless steels (e.g., 316L, 17-4PH): Strength, durability, resistance to oxidation at elevated temperatures.
- Hastelloy and Inconel alloys: Superior corrosion resistance and high-temperature performance. Ideal for aggressive chemical environments and temperatures exceeding 1000°F (538°C).
Secondary seals:
- Flexible graphite: Excellent sealability, thermal conductivity, chemical resistance. Suitable for temperatures up to 1200°F (649°C).
- Grafoil: Similar properties to flexible graphite, can withstand temperatures up to 850°F (454°C).
Mechanical Seal Support Systems for High-Temperature Service
Barrier and Buffer Fluid Systems
A barrier fluid system introduces a compatible liquid between the seal faces, creating a physical barrier between the process fluid and the atmosphere. This barrier fluid is maintained at a higher pressure than the process fluid, preventing process fluid from reaching the seal faces.
In contrast, a buffer fluid system uses a fluid that is compatible with both the process fluid and the seal materials, but at a lower pressure than the process fluid. The buffer fluid helps to cool and lubricate the seal faces, reducing heat generation and extending seal life.
Piping Plans
Piping plans are standardized arrangements of auxiliary equipment and piping that support mechanical seals in various applications, including high-temperature service. These plans are designated by numbers according to the American Petroleum Institute (API) Standard 682. Some common piping plans for high-temperature mechanical seals include:
- Plan 23: This plan uses a heat exchanger to cool the barrier fluid, which is circulated by a pumping ring or external pump. The cooled barrier fluid helps maintain stable temperatures at the seal faces.
- Plan 52: In this arrangement, an external reservoir supplies buffer fluid to the seal chamber through a throttle bushing. The buffer fluid helps to cool and lubricate the seal faces, while the throttle bushing controls the flow rate and maintains the desired pressure differential.
- Plan 53A: This plan combines features of Plans 52 and 23, using a pressurized external reservoir to supply barrier fluid to the seal chamber and a heat exchanger to cool the circulating fluid.
- Plan 54: Similar to Plan 53A, this plan uses an external pressurized reservoir and a heat exchanger, but also includes a close-clearance throttle bushing to control barrier fluid flow and maintain pressure differential.