Mechanical seals play a critical role in protecting equipment and the environment, but single seals often fail to provide adequate protection. Seal failure can lead to leaks, contamination, and costly downtime. Double mechanical seals offer a robust solution, featuring two seals working together with a barrier or buffer fluid to ensure reliable performance and prevent leakage.
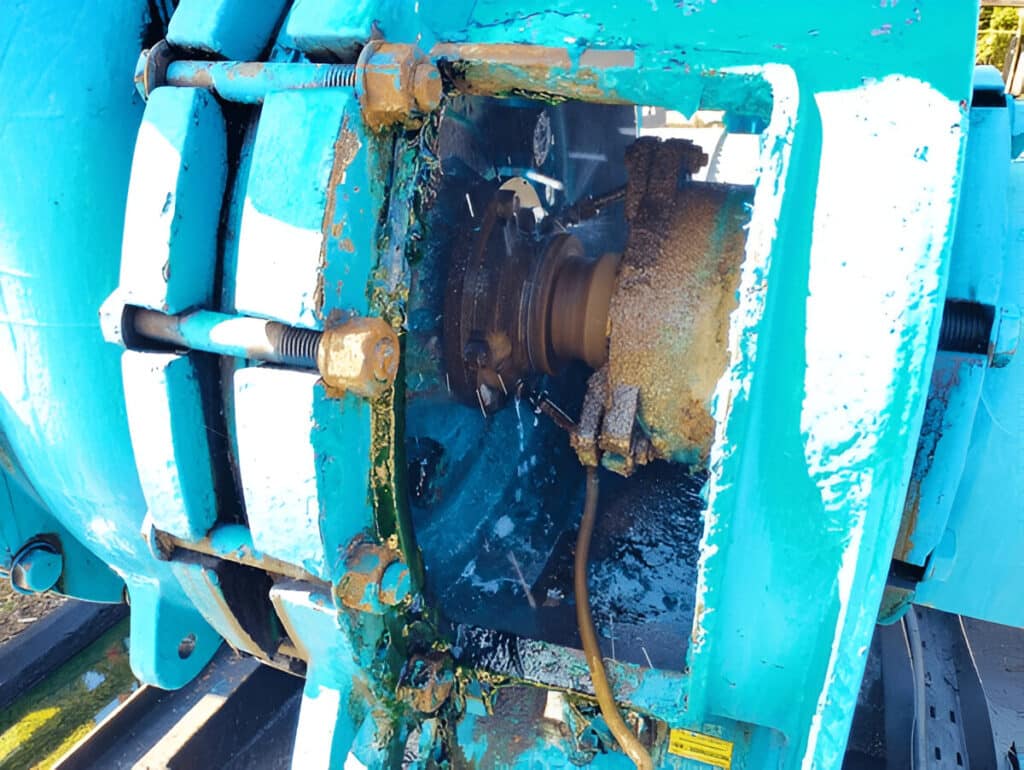
What is a Double Mechanical Seal
A double mechanical seal features two primary seals arranged in series, separated by an intermediary space filled with either a barrier fluid or a buffer fluid.
Each primary seal consists of a stationary face and a rotating face that work together to create a seal. The inner seal, also known as the primary seal, is tasked with containing the process fluid within the equipment, preventing it from leaking into the barrier/buffer fluid area. The outer seal, or secondary seal, serves to prevent the barrier/buffer fluid from escaping into the external environment.
Barrier Fluid and Buffer Fluid
- Barrier Fluid: When the pressure of the intermediate fluid is maintained at a level higher than the pressure of the process fluid, it is referred to as a barrier fluid.
- Buffer Fluid: When the fluid pressure between the seals is intentionally kept lower than that of the process fluid, it is known as a buffer fluid.
Components of Double Mechanical Seals
- Primary (Inner) Seal: This seal, consisting of a rotating face and a stationary face, acts as the first line of defense in preventing process fluid leakage. The rotating face is typically mounted on the shaft or shaft sleeve, while the stationary face is held in place by the seal gland.
- Secondary (Outer) Seal: The outer seal serves as a backup to the primary seal, containing the barrier or buffer fluid between the two seals. Like the primary seal, it features a rotating face and a stationary face.
- Seal Gland: The seal gland is a critical component that houses the seal faces and provides the necessary connections for the introduction and circulation of the barrier/buffer fluid.
- Shaft Sleeves: Shaft sleeves are often used in conjunction with mechanical seals to protect the pump shaft from wear, corrosion, and heat generated by the sealing process. They also help to ensure proper alignment of the seal components.
- Springs: Springs provide the initial closing force on the seal faces, ensuring that they remain in contact even under varying operating conditions.
- Static Seals: O-rings, gaskets, and bellows are used to create static seals between individual components of the seal assembly.
- Hardware Components: Drive rings, retaining rings, and other hardware components secure the seal components in place and facilitating the transmission of torque from the shaft to the rotating seal face.
- Barrier/Buffer Fluid System: The barrier/buffer fluid system consists of a reservoir for storing the fluid, a circulation system (which may include a pump and heat exchanger) to maintain the fluid at the desired temperature and pressure, and pressure control valves to regulate the pressure between the seals.
How Double Mechanical Seals Work
Barrier Mode
In barrier mode, the barrier fluid is maintained at a pressure significantly higher (typically 15-30 psig or 1-2 bar) than the sealed process fluid. This positive pressure differential ensures that if any leakage occurs in the inner seal, it will be the clean barrier fluid that enters the process, effectively preventing hazardous or valuable process fluid from escaping into the atmosphere. This mode offers the highest level of protection against process fluid leakage and is commonly used in applications involving dangerous or expensive fluids.
Buffer Mode
In buffer mode, the buffer fluid is maintained at a pressure lower than that of the sealed process fluid. In this configuration, any minor leakage from the inner seal will be contained within the buffer fluid chamber. The outer seal serves to prevent this potentially contaminated buffer fluid from leaking into the atmosphere. This mode is typically used when some minor leakage from the inner seal is anticipated or acceptable, with the primary concern being to prevent any process fluid from entering the environment.
Fluid Film
Regardless of the mode, the thin fluid film present between the seal faces is maintained by the barrier or buffer fluid. This film provides either hydrodynamic or hydrostatic lubrication, preventing direct contact between the solid surfaces of the seal faces.
Types of Double Mechanical Seals
Back-to-Back Configuration
In a back-to-back arrangement, the two mechanical seals are installed with their rotating seal faces facing away from each other. This configuration creates a sealed chamber between the two seals, which is typically filled with a barrier fluid maintained at a pressure higher than the process fluid pressure.
The back-to-back configuration is well-suited for applications where the primary concern is to prevent process fluid leakage to the atmosphere. The higher-pressure barrier fluid ensures that any leakage will be from the barrier fluid into the process, rather than the other way around.
Tandem Configuration
The tandem configuration, also known as a face-to-face configuration, involves two seals installed in series with their rotating faces facing the same direction. In this arrangement, the space between the two seals is usually filled with a buffer fluid maintained at a pressure lower than the process fluid.
Tandem configurations are often used in applications where some minor leakage from the inner seal is expected or acceptable. The buffer fluid captures any leakage from the inner seal, and the outer seal prevents this fluid from escaping to the atmosphere. Tandem seals can also be used with a barrier fluid at a higher pressure for added protection against process fluid leakage.
Face-to-Face Configuration
In a face-to-face arrangement, the two mechanical seals are positioned with their rotating faces oriented towards each other. This configuration creates a sealed chamber between the two seals that can be filled with either a barrier fluid or a buffer fluid, depending on the application requirements.
Face-to-face configurations offer several advantages, including easier installation and maintenance, as both seals can be accessed from the same side of the equipment. This arrangement also allows for more compact seal designs, making it suitable for applications with limited space.