Pusher and bellow seals are two distinct types of mechanical seals commonly used in rotating equipment across various industries. While both serve the purpose of preventing leakage and contamination, they differ in their design, operation, and application.
This blog post will delve into the key differences between pusher and bellow seals, providing insights into their unique characteristics and suitability for specific industrial requirements.
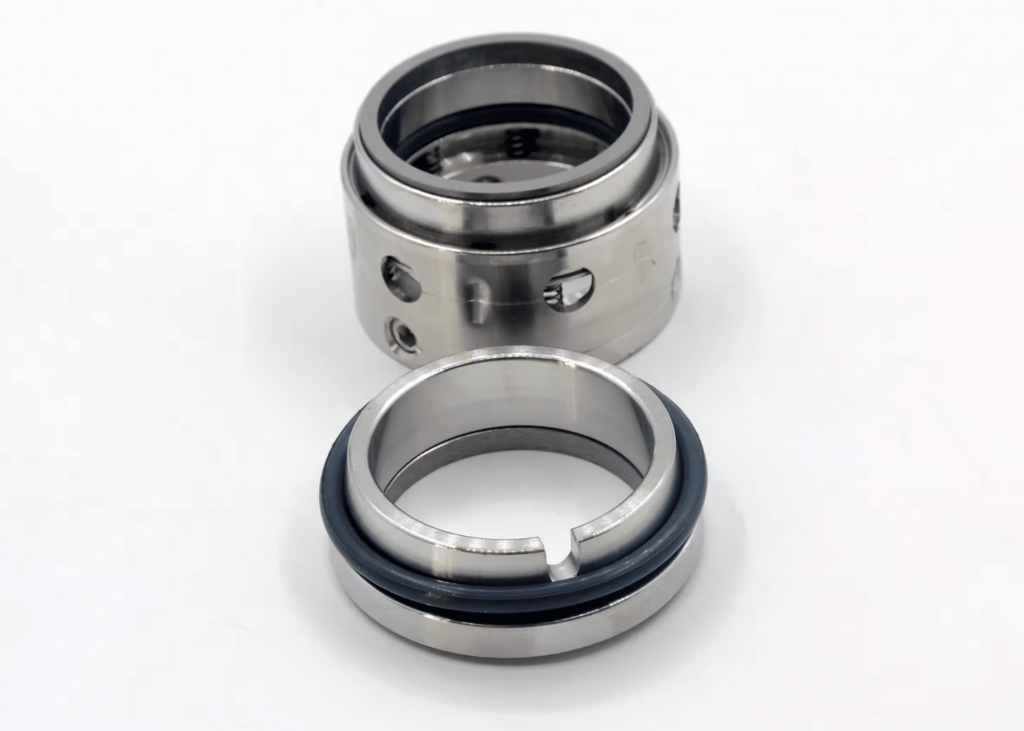
What Is Pusher Seal
A pusher seal, also known as a conventional mechanical seal or non-bellow seal, is a type of mechanical seal commonly used in centrifugal pumps and other rotating equipment. Pusher seals consist of a stationary seal ring and a rotating seal ring that maintain contact to prevent fluid leakage. The sealing surfaces are kept in contact by a secondary sealing element, typically a single coil spring or multiple springs, that provides the necessary closing force.
The secondary sealing element in pusher seals is usually an O-ring or V-ring made from elastomeric materials such as Buna-N rubber. These secondary seals play a crucial role in accommodating shaft misalignment and axial shaft movement. However, the elastomeric components have limited chemical compatibility and temperature range compared to other seal designs.
Pusher seals can be either balanced or unbalanced, depending on the application requirements. Balanced pusher seals have a balance ratio that reduces the closing force on the sealing surfaces, making them suitable for high-pressure applications. Unbalanced seals, on the other hand, are commonly used in low-pressure applications or when the sealed fluid is not hazardous.
What Is Bellow Seal
A bellows seal, also known as a metal bellows seal or non-pusher seal, is a type of mechanical seal that uses a thin-walled metal bellows as the secondary sealing element. The metal bellows, typically made from stainless steel or other corrosion-resistant alloys, provides a flexible and durable sealing component that eliminates the need for elastomeric secondary seals.
In a bellows seal, the metal bellows is welded to the stationary seal ring and the seal housing, creating a secure and leak-tight seal. The bellows acts as both the secondary seal and the spring element, providing the necessary closing force to maintain contact between the sealing surfaces. As the bellows is compressed, it generates a spring load that keeps the primary sealing faces in contact.
Key Differences Between Pusher and Bellow Seals
Secondary Seal Type
Pusher seals typically utilize O-rings or other elastomeric components as secondary seals. These secondary seals are designed to provide a secure seal between the stationary and rotating parts of the seal assembly.
In contrast, bellow seals feature a metal bellows assembly that serves as both the secondary seal and the spring element. The bellows provides a leak-tight seal while also accommodating axial shaft movement and misalignment.
Pressure Capability
Pusher seals are generally suitable for low to moderate pressure applications, with a typical pressure limit of around 20 bar. They can handle higher pressures when designed as double seals or with additional springs.
On the other hand, bellow seals excel in high-pressure environments. The metal bellows design allows for a higher pressure capability, often exceeding 100 bar.
Temperature Range
Pusher seals are commonly used in applications with moderate temperature requirements, typically up to 150°C. The elastomeric secondary seals used in pusher seals limit their high-temperature suitability.
In contrast, bellow seals can withstand much higher temperatures due to their all-metal construction. With appropriate materials like stainless steel or Hastelloy, bellow seals can operate in temperatures exceeding 400°C.
Maintenance Needs
Pusher seals often require more frequent maintenance due to the wear and degradation of the elastomeric secondary seals.
Bellow seals, on the other hand, have lower maintenance needs. The all-metal construction eliminates the need for periodic replacement of secondary seals.
Application Suitability
Pusher seals are commonly used in general-purpose applications with moderate pressure and temperature conditions. They are cost-effective and suitable for a wide range of fluids, including water, oils, and mild chemicals. Pusher seals find extensive use in industries such as water treatment, pulp and paper, and food processing.
Bellow seals, with their superior pressure and temperature capabilities, are preferred for more demanding applications. They excel in handling high-pressure, high-temperature, and corrosive media. Bellow seals are commonly found in the oil and gas industry, chemical processing plants, refineries, and power generation facilities. They are also suitable for applications involving high-purity fluids or where minimal leakage is critical, such as in the pharmaceutical and semiconductor industries.