The main categories of agitator seals include mechanical seals, lip seals, and packing or stuffing box seals. Mechanical seals, the most common type, can be further classified into dry gas seals, liquid-lubricated seals, and wet seals, depending on their sealing mechanism and barrier fluid.
When selecting an agitator seal, it is essential to consider various factors such as operating conditions, process fluid properties, seal compatibility, leakage and emissions requirements, initial and operating costs, and maintenance and reliability. By carefully evaluating these aspects, you can choose the most suitable seal type for your specific application, ensuring optimal performance and longevity of your agitation equipment.
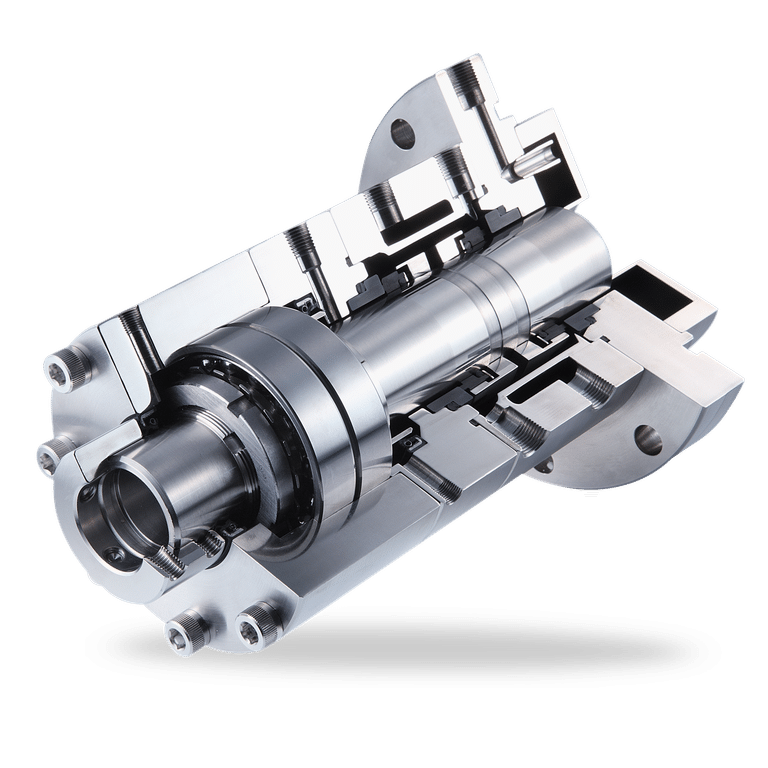
Types of Mechanical Seals for Agitators
Dry Gas Seals
Dry gas seals utilize a pressurized gas, such as nitrogen or air, as a barrier between the process fluid and the atmosphere. The gas is introduced between the precision-machined carbon seal faces, creating a thin, non-contacting gas film that prevents leakage. Dry gas seals are ideal for applications with low to medium pressures and temperatures, offering low friction and wear, as well as reduced maintenance requirements compared to other seal types.
Liquid-Lubricated Seals
Liquid-lubricated seals, also known as wet seals, employ a pressurized liquid barrier fluid to lubricate and cool the seal faces. The barrier fluid, typically a compatible oil or glycol-based solution, is maintained at a higher pressure than the process fluid to prevent leakage. Liquid-lubricated seals are essential for high-pressure and high-temperature applications, as they provide better heat dissipation and pressure resistance compared to dry gas seals.
Wet Seals
Wet seals are a type of liquid-lubricated seal that continuously circulate the barrier fluid through the seal faces. The circulation helps maintain a stable fluid film between the faces, reducing wear and heat generation. In some cases, a seal-mounted or external pump is used to assist the circulation, ensuring optimal barrier fluid flow and pressure. Wet seals are suitable for demanding applications with high pressures, temperatures, or abrasive process fluids, offering enhanced reliability and extended seal life.
Configurations of Mechanical Seals for Agitators
Single Seals
Single mechanical seals for agitators consist of a single set of sealing faces, typically made of hard-wearing materials like silicon carbide or tungsten carbide. This configuration offers a simpler, more compact design compared to other types of agitator seals. However, single seals have a higher risk of leakage since there is no backup sealing mechanism in case of primary seal failure.
Double Seals
Double mechanical seals for agitators feature two sets of sealing faces, providing an additional layer of protection against leakage. If the primary seal fails, the secondary seal serves as a backup, ensuring continued sealing and containment of the process fluid. Double seals are ideal for applications involving hazardous or environmentally sensitive fluids where leakage must be minimized.
Tandem Seals
Tandem mechanical seals for agitators have their sealing faces arranged in series, allowing them to withstand higher pressures compared to single or double seals. In this configuration, the primary seal faces the process fluid, while the secondary seal acts as a backup. Tandem seals are suitable for high-pressure applications or when dealing with abrasive or corrosive fluids that may cause premature wear on a single seal.
Dual Pressurized Seals
Dual pressurized mechanical seals for agitators consist of two independent seals with a barrier fluid circulating between them. The barrier fluid, typically a compatible liquid or gas, maintains a higher pressure than the process fluid, preventing leakage and providing lubrication and cooling to the seal faces. Dual pressurized seals offer excellent reliability and are commonly used in critical applications where seal failure cannot be tolerated.
Other Agitator Seal Types
Lip Seals
Lip seals, also known as radial shaft seals, are a type of agitator seal that consists of an elastomeric material designed to fit tightly around the shaft. These seals are typically made from materials such as nitrile, silicone, or fluoroelastomers, which provide good chemical resistance and flexibility. Lip seals are designed to prevent leakage by maintaining constant contact with the shaft surface.
However, lip seals are only suitable for low-pressure applications due to their limited ability to withstand high pressures. They are commonly used in applications where the process fluid is not hazardous or corrosive and where a small amount of leakage is acceptable. Lip seals are relatively inexpensive and easy to install, making them a cost-effective option for low-pressure agitator sealing applications.
Packing or Stuffing Box Seals
Packing or stuffing box seals are one of the oldest types of agitator seals, dating back to the early days of industrial machinery. These seals work by compressing a packing material, such as braided graphite, PTFE, or aramid fibers, around the shaft to create a tight seal. The packing material is held in place by a gland follower, which is adjusted to maintain the proper compression.
Packing seals are known for their simplicity and reliability, as they do not require complex components or barrier fluids. However, they are prone to wear and leakage over time, as the packing material gradually loses its compressibility and sealing ability. Regular maintenance, including adjusting the gland follower and replacing the packing material, is necessary to ensure optimal performance.
While packing seals have largely been replaced by more advanced sealing technologies in many applications, they remain a viable option for low-pressure, low-speed agitator sealing applications where a small amount of leakage is acceptable. Packing seals are also relatively inexpensive and easy to maintain, making them a cost-effective choice for certain industrial applications.
Factors to Consider When Selecting an Agitator Seal
Operating Conditions
When choosing an agitator seal, it’s essential to evaluate the operating conditions of your specific application. The seal must be capable of withstanding the pressure, temperature, and shaft speed present in the system. Higher pressures and temperatures may require more robust seal materials and designs, such as double or tandem seals.
Process Fluid Properties
The properties of the process fluid play a crucial role in seal selection. Viscosity, pH, abrasiveness, and cleanliness requirements can impact seal performance and longevity. For example, highly viscous fluids may require special seal faces to prevent leakage, while abrasive particles can cause premature wear on seal components.
Seal Compatibility
Agitator seals must be compatible with the process fluid and operating environment. Chemical resistance is a key factor, as the seal materials must withstand exposure to the specific chemicals present without degradation. Temperature limits of the seal materials should also be considered, ensuring they can handle the expected temperature range. In food and pharmaceutical applications, seals may need to be constructed from FDA-approved, food-grade materials to maintain product purity and safety.
Leakage and Emissions Requirements
Different industries and applications have varying requirements for allowable leakage rates and emissions. Some processes may tolerate minor leakage, while others demand near-zero emissions to meet environmental regulations or maintain product quality. Consider the specific leakage and emission requirements for your application when selecting an agitator seal. Additionally, determine if any monitoring needs, such as leak detection systems, are necessary to ensure compliance and safety.
Initial and Operating Costs
The total cost of ownership should be evaluated when choosing an agitator seal. Initial costs include the seal price and installation expenses, while operating costs encompass factors such as barrier fluid consumption, energy consumption, and maintenance requirements. Liquid-lubricated seals, for instance, require a continuous supply of barrier fluid, which can add to ongoing expenses.
Maintenance and Reliability
Seal life expectancy, repair requirements, and the availability of spare parts can significantly impact overall equipment effectiveness and maintenance costs. Opt for seals with proven reliability and extended service life to minimize downtime and maintenance interventions. Consider the ease of repair and the availability of spare parts to ensure quick recovery in the event of a seal failure. Regular maintenance, such as barrier fluid monitoring and seal face inspections, can help extend seal life and prevent unplanned downtime.
FAQs
How do mechanical seals work in agitators?
Mechanical seals consist of two flat surfaces (one stationary, one rotating) that are pressed together by springs or bellows. A thin film of fluid between the surfaces provides lubrication and prevents leakage.
What are the advantages of using lip seals in agitators?
Lip seals are simple, cost-effective, and easy to install. They are suitable for low-pressure applications and can handle moderate misalignment and shaft runout.
When are packing glands used in agitators?
Packing glands are used in low-pressure, low-speed applications where some leakage is acceptable. They are commonly found in older agitator designs and are gradually being replaced by mechanical seals.
Can agitator seals be repaired, or do they need to be replaced?
In most cases, agitator seals need to be replaced when they fail or reach the end of their service life. However, some mechanical seals can be repaired by replacing worn components, such as O-rings or springs.
How often should agitator seals be inspected and maintained?
Agitator seals should be inspected regularly (e.g., monthly) for signs of wear, leakage, or damage. The frequency of maintenance depends on the type of seal and the operating conditions, but generally, seals should be replaced every 1-2 years or as recommended by the manufacturer.
Can different types of agitator seals be used interchangeably?
In general, different types of agitator seals are not interchangeable, as they are designed for specific applications and operating conditions. It is essential to select the appropriate seal type based on the requirements of the agitator and the process.