Mechanical seals are essential components in a wide variety of industrial applications, particularly in centrifugal pumps and other equipment involving rotating shafts. The primary function of a mechanical seal is to prevent the leakage of process fluid from the pump housing while allowing the shaft to rotate freely. To achieve this, mechanical seals rely on several critical sealing points, which can be classified as either dynamic or stationary.
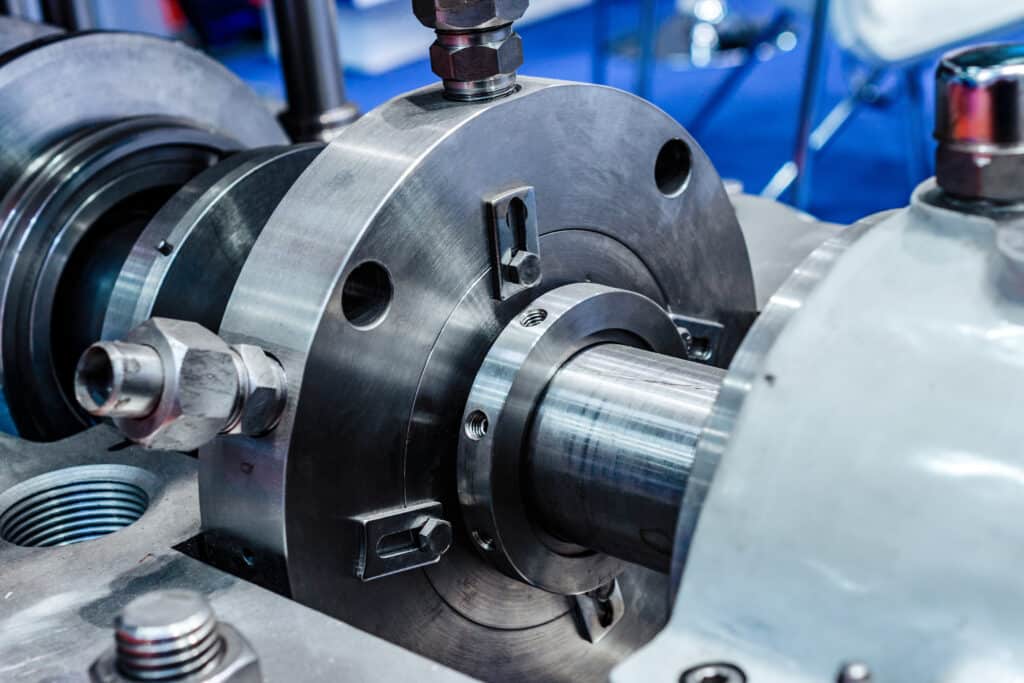
What is Sealing Point
In the context of mechanical seals, a sealing point refers to the interface between two components where a seal is formed to prevent fluid leakage. The effectiveness of a mechanical seal depends on the integrity of these sealing points, which must withstand the pressure, temperature, and chemical composition of the process fluid, as well as the rotational forces generated by the shaft.
Sealing points in mechanical seals can be categorized into two main types: dynamic sealing points and stationary sealing points. Dynamic sealing points are those where one sealing surface rotates relative to the other, while stationary sealing points involve two non-moving surfaces.
How Many Sealing Points Does a Mechanical Seal Have
A mechanical seal has 4 sealing points. One is the dynamic sealing point. The others 3 are the stationary sealing points. These 4 points work together to prevent leaks.
Dynamic Sealing Point
The dynamic sealing point is the most critical component of a mechanical seal, as it is responsible for maintaining a fluid-tight barrier between the rotating shaft and the stationary seal components. This sealing point consists of two main components: the primary sealing element, which is typically a pair of flat, annular surfaces (one stationary and one rotating) that are pressed together by a spring or other means, and the secondary sealing elements, which are usually O-rings or other elastomeric seals that prevent leakage between the stationary and rotating components of the seal assembly.
The dynamic seal interface is the point of contact between the rotating and stationary seal faces. These faces are lapped to a very high degree of flatness and are typically made from hard, wear-resistant materials such as silicon carbide, tungsten carbide, or ceramic. The seal faces are designed to run against each other with a thin film of fluid between them, which helps to lubricate and cool the sealing surfaces.
Stationary Sealing Points
In addition to the dynamic sealing point, mechanical seals also rely on several stationary sealing points to prevent fluid leakage. These sealing points are located between the non-moving components of the seal assembly and the pump housing.
Seal to Shaft Sealing
The seal-to-shaft sealing point is responsible for preventing fluid leakage between the rotating shaft and the stationary components of the seal assembly. This sealing point typically consists of a shaft sleeve or collar that is attached to the shaft and rotates with it, and a stationary sealing element that is pressed against the sleeve by a spring or other means.
The shaft sleeve is usually made from a hard, wear-resistant material such as stainless steel or ceramic, and it may be coated with a specialized surface treatment to enhance its resistance to abrasion and corrosion. The stationary sealing element is typically an O-ring or other elastomeric seal that is designed to maintain a tight, fluid-tight fit against the shaft sleeve.
Seal to Housing Sealing
The seal-to-housing sealing point is responsible for preventing fluid leakage between the stationary components of the seal assembly and the pump housing. This sealing point typically consists of a gasket or O-ring that is compressed between the seal gland plate and the pump housing, creating a fluid-tight barrier.
The gasket or O-ring material must be compatible with the process fluid and capable of withstanding the operating temperatures and pressures encountered in the application. In some cases, specialized gasket materials or designs may be used to enhance the sealing performance or to accommodate thermal expansion or other dimensional changes.
Gland Plate to Stuffing Box Sealing
The gland plate-to-stuffing box sealing point is responsible for preventing fluid leakage between the gland plate and the stuffing box, which is the cavity in the pump housing where the seal assembly is installed. This sealing point typically consists of a gasket or O-ring that is compressed between the gland plate and the stuffing box face.
As with the seal-to-housing sealing point, proper selection of gasket material and correct installation and tightening of the gland plate bolts are essential to ensure an effective seal. In some cases, a split gland plate design may be used to facilitate seal installation and maintenance, particularly in applications where frequent seal replacement is required.