API mechanical seals are a critical component in rotating equipment, ensuring reliable and safe operation in demanding industrial applications. Adhering to the API 682 standard, these seals come in various types and arrangements to suit specific machinery requirements.
This article explores the intricacies of API mechanical seals, delving into the API 682 standard, seal types and arrangements, support systems, piping plans, selection criteria, and the benefits they offer. By understanding these aspects, professionals in the machinery industry can make informed decisions when selecting and implementing API mechanical seals in their equipment.
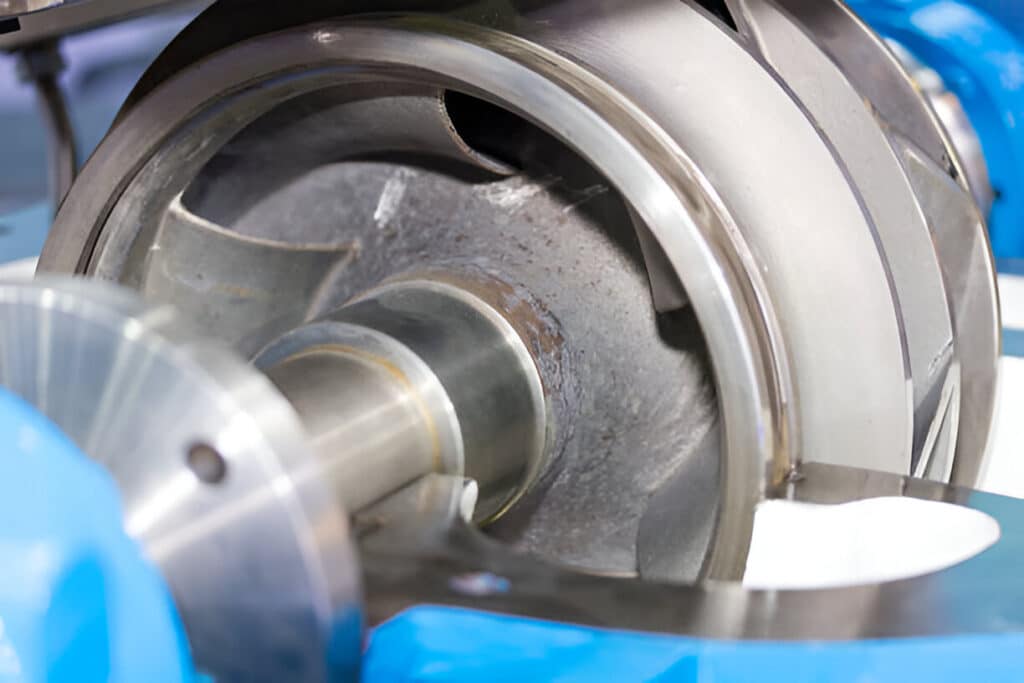
What Is API Standard 682
API Standard 682 is a globally recognized standard developed by the American Petroleum Institute (API) that establishes requirements and provides guidelines for the selection, design, specification, and operation of sealing systems used in centrifugal and rotary pumps in the petroleum, natural gas, and chemical industries. This comprehensive standard covers multiple aspects of mechanical seals, including seal types, configurations, materials, support systems, and auxiliary piping plans.
The primary objective of API 682 is to facilitate the standardization of mechanical seals and associated equipment, ensuring reliability, safety, and interchangeability across various applications. By adhering to this standard, manufacturers, suppliers, and end-users can benefit from improved seal performance, reduced downtime, and lower maintenance costs.
API 682 has undergone several revisions since its initial publication in 1994, with the latest edition being the 4th edition, released in 2014. Each revision incorporates updates and improvements based on industry feedback, technological advancements, and operational experience.
Types and Arrangements of API Mechanical Seals
Seal Types
API 682 defines three main types of mechanical seals:
- Type A: Pusher Seals
- Designed for general-purpose applications
- Consist of a rotating primary ring and a stationary mating ring
- Utilizes springs or bellows to maintain sealing contact
- Type B: Metal Bellows Seals
- Employ a metal bellows to provide axial movement and maintain sealing contact
- Suitable for high-temperature and high-pressure applications
- Offer enhanced leakage control and stability compared to pusher seals
- Type C: Non-Pusher Seals
- Encompass a variety of designs, such as elastomeric bellows seals and high-pressure seals
- Provide specific capabilities for unique application requirements
Seal Arrangements
API 682 defines three primary seal arrangements:
- Arrangement 1: Single Seal
- Consists of a single seal assembly
- Suitable for non-hazardous, non-volatile, or non-toxic fluids
- Requires a seal flush to maintain clean and cool sealing surfaces
- Arrangement 2: Dual Unpressurized Seals
- Employs two seal assemblies with a buffer fluid between them
- Buffer fluid maintains a higher pressure than the sealed fluid, preventing leakage to the atmosphere
- Provides enhanced safety and reliability compared to single seals
- Arrangement 3: Dual Pressurized Seals
- Similar to Arrangement 2 but with a pressurized barrier fluid between the seal assemblies
- Barrier fluid pressure is maintained at a higher level than the sealed fluid pressure
- Offers the highest level of safety and emission control, suitable for hazardous or environmentally sensitive applications
Seal Support Systems
Seal support systems are designed to provide the necessary environmental conditions for mechanical seals to function properly. These systems maintain the required pressure, temperature, and lubricating fluid for the seal faces. The most common seal support systems include:
- API Plan 11: Used for single seals, this plan incorporates a seal fluid reservoir and provides a higher pressure than the process fluid to maintain a positive flow into the seal chamber.
- API Plan 21: This plan is used for double seals and includes a seal fluid reservoir pressurized by an external source, such as nitrogen gas, to maintain a constant pressure on the seal faces.
- API Plan 53: Designed for double seals, this plan features a barrier fluid circulating system with a heat exchanger and pressure control to maintain optimal conditions for the seal faces.
Piping Plans
API piping plans are standardized arrangements of piping, instrumentation, and equipment used to support mechanical seals. These plans ensure that the seal is provided with the proper fluid environment for reliable operation. Some common piping plans include:
- API Plan 01: A basic plan that vents the seal chamber to a safe location, typically used for non-hazardous fluids.
- API Plan 02: This plan uses a throttle bushing to control the flow of the process fluid to the seal chamber, providing cooling and lubrication to the seal faces.
- API Plan 23: Designed for double seals, this plan circulates a barrier fluid between the inner and outer seals using a pumping ring, providing cooling and lubrication to the seal faces.
Selection Criteria
When selecting an API mechanical seal for a specific application, several factors must be considered to ensure optimal performance and reliability:
Process Fluid Properties
The properties of the process fluid, such as its chemical composition, temperature, pressure, and viscosity, must be evaluated to determine the most suitable seal materials and design.
Operating Conditions
The operating conditions of the equipment, including speed, load, and environmental factors, should be taken into account when selecting a mechanical seal to ensure it can withstand the demands of the application.
Seal Arrangement
The seal arrangement (single, double, or tandem) should be chosen based on the level of redundancy and safety required for the specific application.
Material Compatibility
The materials used in the mechanical seal must be compatible with both the process fluid and the surrounding environment to prevent corrosion, degradation, or premature failure.
Benefits of Using API Mechanical Seals
API mechanical seals offer several advantages over other sealing methods, making them a preferred choice for many industries:
Improved Reliability
API mechanical seals are designed and manufactured to strict quality standards, ensuring consistent performance and longer service life compared to non-API seals.
Enhanced Safety
By adhering to API standards, mechanical seals minimize the risk of leaks and failures, reducing the potential for hazardous situations and environmental contamination.
Increased Efficiency
API mechanical seals are engineered to minimize friction and wear, resulting in lower energy consumption and improved overall system efficiency.
Standardized Design
The standardized design of API mechanical seals allows for easier maintenance, repair, and replacement, reducing downtime and associated costs.